In this new weekly blog series, NRM will highlight an issue a customer had and was able to resolve with our industry-leading control and monitoring solutions. Some of the most serious refrigeration problems can go undetected and result in equipment failures and/or product loss.
Problem of the Week: Pesky Solenoid Valve is Stuck Open Again
As is often the case with large, complex systems that we don’t personally have the appropriate knowledge or training for, owners/operators, mangers, and regular staff usually regard their business’ commercial or industrial refrigeration equipment with an “out of sight, out of mind” mentality. Without the necessary technical expertise to professionally diagnose a problem, they either pay the system little to no attention, or interact with it and don’t consider the consequences (because they’re not aware any exist). This can often lead to many, expensive service calls or, worse, an issue that can not only degrade the equipment but ruin it.
This new blog series, NRM’s Refrigeration Problem of the Week, will take a look at real-world situations where unique control and monitoring tools averted disaster for a business.
For today’s post, we take a look at a problem that many of our clients deal with: repetitive failure of a mechanical component. Sometimes, it’s the way the piece was installed into the system, and sometimes it’s just from a bad batch. Either way, it’s the type of issue that may be noticed once, remedied, and then forgotten about all over again. For a smaller facility that only has one condenser dedicated to the cold room–say, a walk-in beverage cooler in a convenience store–it would be easier to spot if a replaced component failed again. But a facility that has multiple cold rooms, or multiple condensers dedicated to a space, the issue would be much harder to detect.
One of our clients, as a result of implementing NRM’s monitoring platform, was alerted to a stuck solenoid valve on a Tuesday. Notifications went out to multiple, designated employees instantly. They contacted their dedicated service technician, who was able to come out that day and troubleshoot. The technician located the cause of the issue and replaced a faulty washer. Restarting the refrigeration system, and consulting the performance trends in the monitoring platform’s online dashboard, it appeared as if everything was back to normal.
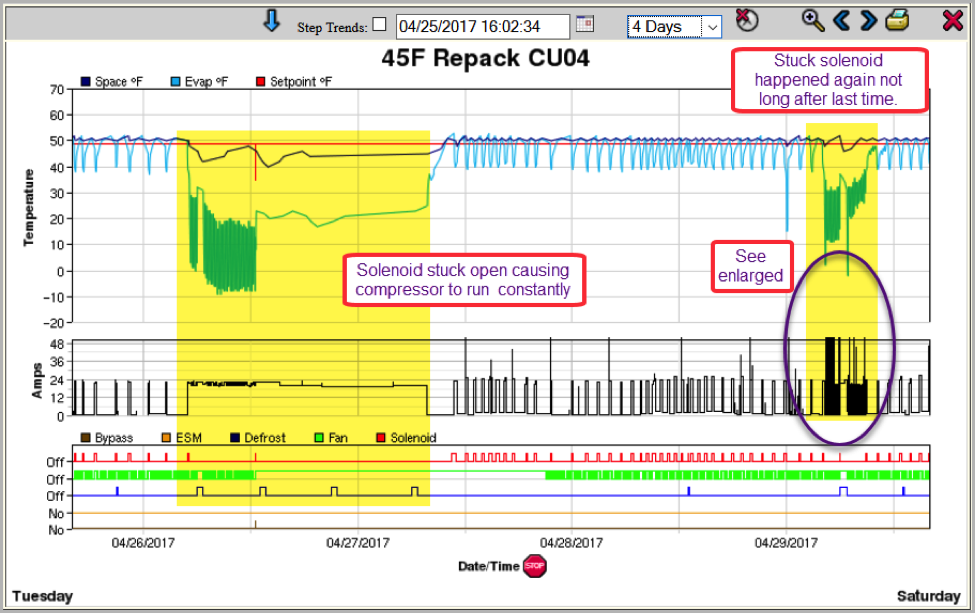
As you can see in the performance trend below, the issue came back on a Saturday (the worst possible time for an issue for a M-F business). It caused the compressor to run constantly, temperatures to fluctuate, and short cycling. Without NRM’s monitoring tools, the issue would’ve gone unnoticed for a full weekend, risking both equipment and product.
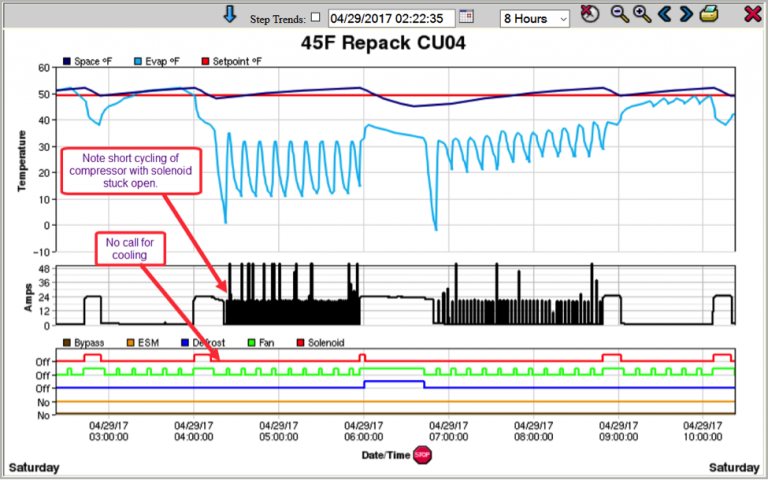
The client’s technician wound up having to replace the entire valve, and this finally remedied the problem.