Now that we know what electric defrost is, how it works and how much it costs—it’s time to talk about how to use it more efficiently by implementing several control strategies. Electric defrost is a necessity to keep commercial walk in freezers working properly, but it can also be an energy guzzler if over used.
The good news is that there are ways to tame those extra costs. Here are some time tested solutions to perform defrosts more efficiently and help gain control.
We previously discussed that defrost timers are commonly scheduled for worst case conditions, which means that defrost is being performed when there is no, or minimal frost, wasting energy. Technicians aren’t wrong by scheduling a few extra defrosts. If defrosts are not performed when needed, it can result in a new and potentially worse problem. If a coil isn’t defrosted, coil efficiency and system performance are compromised since the ice is blocking air flow. There’s an added risk of sending liquid back to the compressor and then really bad things can happen to the compressor components.
Now, let’s talk about proven strategies that save energy without putting cooling performance or equipment at risk.
1) Thermostatic Defrost
Advanced programmable electronic controls have become readily available and at much lower cost. It has been applied to industrial process control where complex control strategies can be easily configured and implemented.
By observing real time defrosts and analyzing historical operation, new strategies were developed through a trial and error process to optimize the process. Instead of defrosting by a termination process at a very high temperature we implemented a thermostatically controlled defrost which includes:
- Installing a temperature probe in the evaporator coil to manage and control the defrost process.
- Setting and tuning the duration of a defrost event and allowing the defrosting period to last the full time period set. Can be done remotely over web with real time view of defrost.
- Setting the maximum temperature the coil can reach during defrost and cycling the heaters OFF and ON to maintain that maximum temperature throughout the defrost duration. (This is usually much lower than typical termination temperature using mechanical sensor.)
The following screen captures show traditional (Figure 1 – Before) and thermostatically controlled (Figure 2 – After) defrost profiles.
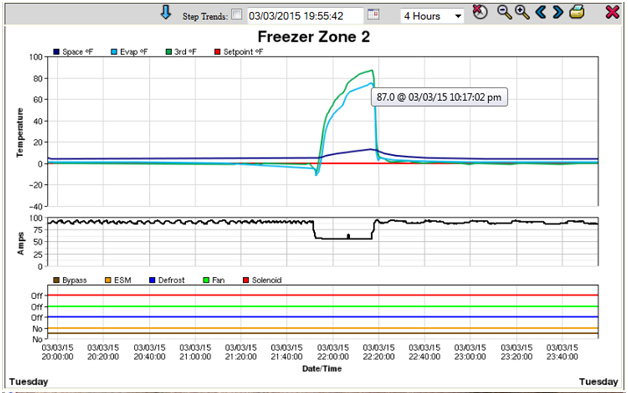
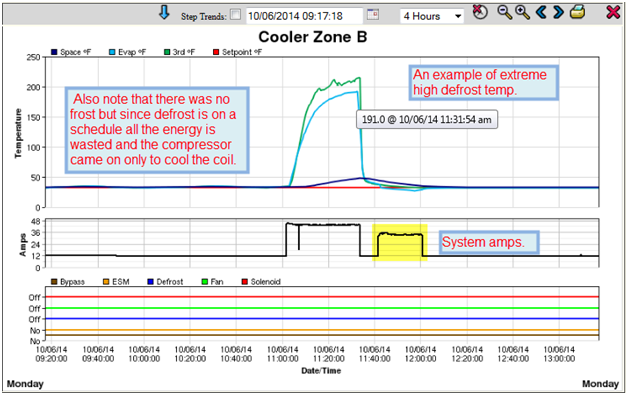
Figure 1 – Before: Note the Peak Temperature at which defrost terminated.
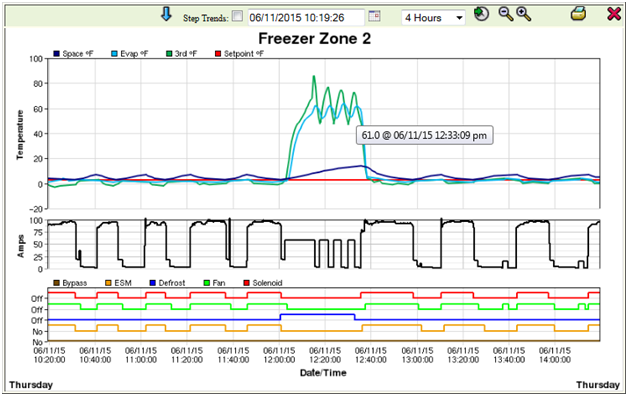
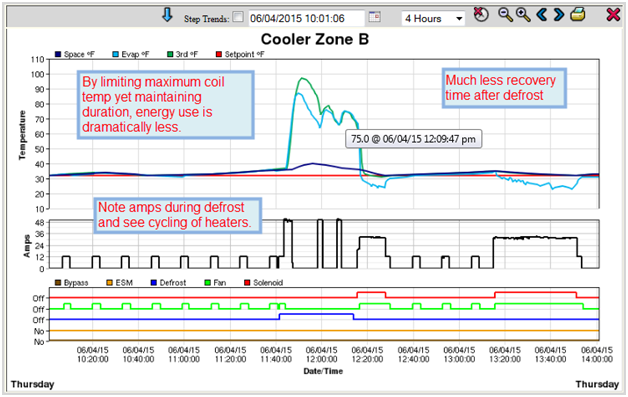
Figure 2 – After: Note the lower Peak Temperature at which defrost temp is maintained.
When comparing the two figures it is easy to realize that a thermostatically managed electric defrost can yield at least 30% energy savings.
2) Optimizing Defrost Schedule
In many cases the number of defrosts may be reduced. As an example, in the case of the Freezer Zone 2 above the number of defrosts per day were reduced from 4 to only 2 thus saving even more energy. As another example, typical time clocks call for set schedules every day, 7 Days a week. Real time monitoring and control systems allow you to modify defrost schedules for non-workings days like Saturdays and Sundays and during holidays. So when combining thermostatically controlled defrost and optimizing the defrost schedule, we have seen owners save 30% up to 70% of the energy required for electric defrost.
3) Smart Defrost or Defrost On-Demand
When real time viewing is possible, an owner or technician can further reduce energy and optimize defrosts by employing Smart Defrost or Defrost On-Demand.
Smart Defrost strategy results in better refrigeration performance since defrost activation is based on need, not on time. In some cases, more defrosts are performed during heavy loading conditions and fewer defrost are performed when there is little to no activity in the cold room.
There are some cases where there were 7 or more defrosts required in a day, while in other cases only one defrost every 2 days (See Figure 3). It is easy to understand that on nights and weekends few to no defrosts are required, while during regular work days more defrosts are needed.
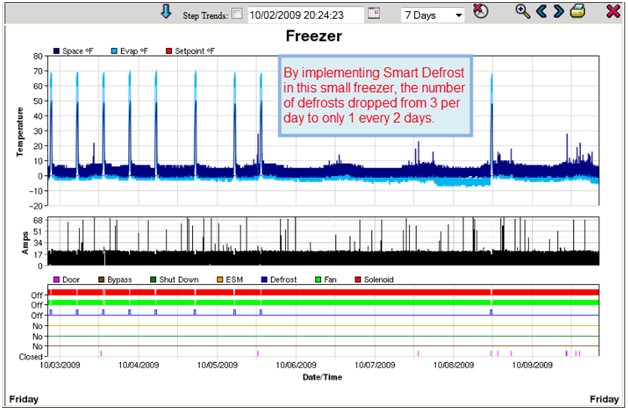
In summary, intelligent controls can be calibrated for each system to perform a more energy efficient electric defrost:
- Thermostatic defrost: regulates the temperature of the heater elements by cycling the heaters on and off during defrost so as not to exceed specified coil temperature. This results in a reduction of heater runtime by up to 60% and minimizes the amount of heat spilled into the space.
- Optimizing defrost schedule: instead of setting the number of defrosts for worst case, program defrost schedules as needed based on actual operation during working and nonworking periods. When using real time clock for defrosting it is a good idea to adjust based on seasonality so fewer defrosts are performed during cooler months and more during warmer months.
- On-Demand Defrost: initiates a defrost cycle only when the coil needs to be defrosted for 50%-75% savings.