In commercial applications, one of the most important tasks in keeping components running at their peak performance is determining what’s a cause and what’s a symptom if mechanical problems arise. The difference between knowing and not knowing could be thousands of dollars worth of diagnosis.
In particular, short cycling seems to be one of those refrigeration and HVAC terms that gets murkier the deeper you get into the water. This blog post will explain what short cycling is, why it’s harmful for your system, and what issues it is born from.
First thing’s first: what is short cycling?
Short cycling occurs in your compressor when a mechanical failure is causing the run times to terminate prematurely and since set point has not been achieved, it restarts shortly afterward, thus requiring more compressor ‘ON’ time to compensate. Short cycling is a symptom of a potentially wide range of causes. Think of short 2-5 minute bursts of ON and OFF times that can go on for days, weeks and months before the condition is noticed.
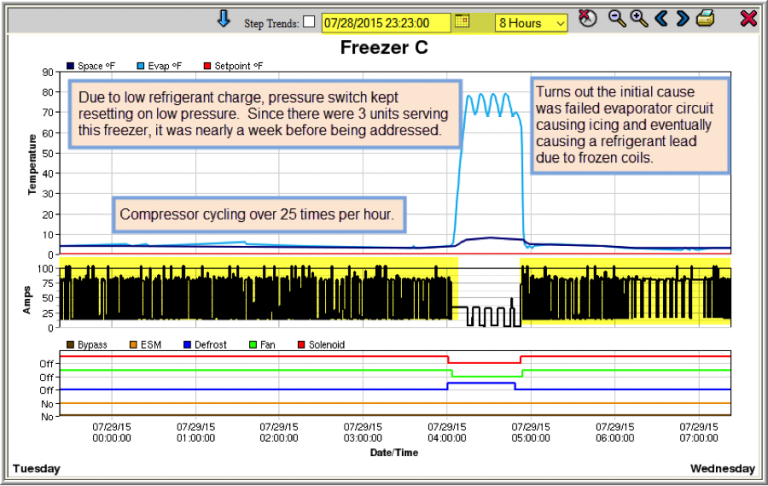
Because short cycling is usually a sign of a larger issue, it’s important that a technician is able to uncover the root cause as opposed to simply replacing parts or repairing components. These are band-aid fixes and while they may buy you some extended life on your cooling system, it still leaves open the potential for a complete system failure.
“Any time a compressor has failed, a technician needs to find the root cause and correct it before the replacement compressor fails as well. This is not always an easy task, but it is an important part of the service provided to a customer. Having the replacement compressor fail due to an unresolved system issue is not good for the technician, his company, or the customer.1”
“If a compressor fails prematurely (<15 years old), first consider why the unit died in the first place. Don’t simply replace the compressor, override a safety and/or apply a band-aid just to get it running again. Odds are, the failure will occur again, perhaps with worse consequences, and surely with wasted expense.2”
In addition to repair costs, any compressor that is short cycling will consume a great deal more energy and the controlled space rarely reaches set point. Operating in this condition can consume 20-50% more energy a hidden cost that is rarely linked to the problem.
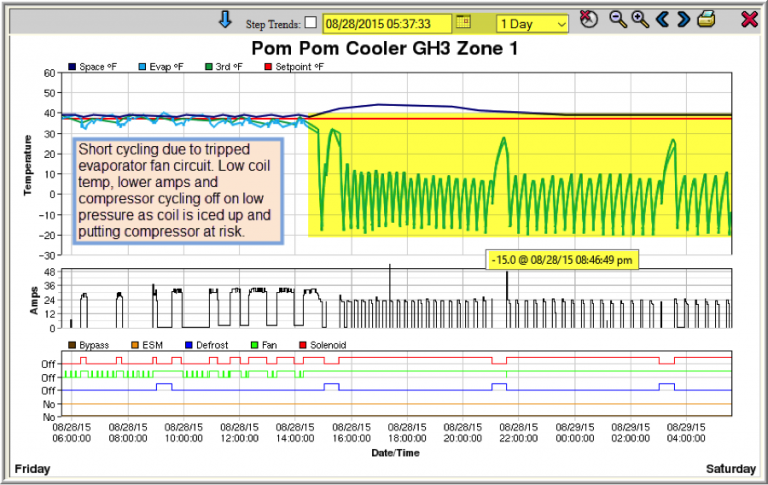
So now that we know what short cycling is and why it’s important to undertake a thorough diagnosis if it occurs, here are the most common causes (look out for these!):
Low refrigerant/oil mixture: Every time a compressor cycles, a small amount of oil that is supposed to keep it lubricated actually travels as a mixture with the refrigerant throughout the system. “If the compressor is cycled off and on too quickly, an imbalance is created. Each time the compressor starts, oil is pumped out, but without sufficient run time the oil stays out in the system and does not return to lubricate the compressor. This imbalance will lead to a shortage of oil inside the compressor and bearing failure1.”
Dirty condenser/automatic high pressure reset: With the daily juggling act that business owners face every time they flip the OPEN sign, as long as the compressor is functioning in some capacity, being proactive in the system’s performance or maintenance rarely sees priority status. A dirty condenser can severely limit your system’s ability to reject heat for regulating temperatures and pressures needed for cooling which can lead to compressor tripping on high head pressure. If the condenser has automatic high pressure reset it can result in short run cycles.
High Condenser discharge pressure due to air recirculating: If the condenser is in a confined area where the air used to cool the condenser is recirculated the temperature and pressure will rise causing high pressure reset and short cycling. Usually observed when a condenser is in a basement or attic area and the heat from the condenser heats the air and as it is recirculated it overheats the condenser causing a high pressure trip and reset.
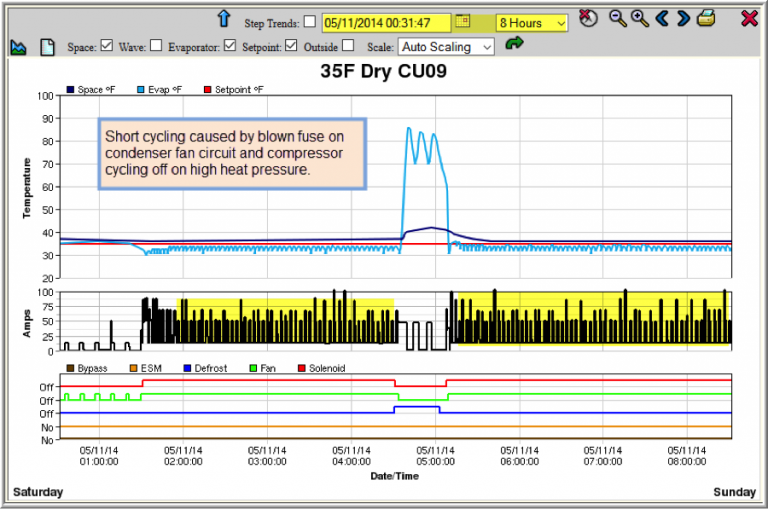
Pressure or temperature control differential is too small: When the pressure controller’s low pressure differential is set too tight, it can cause the compressor to short cycle. This can be observed during normal cooling when the low pressure setting is reached and the compressor cycles off until the pressure in the evaporator rises above the high side of the low pressure setting. This results in longer times to achieve set point and greater energy use.
Lack of operation time delay: While it’s certainly important to have a minimum and maximum run time in place for proper system performance, it’s equally important to have a minimum OFF time in the form of an operation time delay. This is arguably the most common cause of a short cycle. By having an effective time delay, you can potentially prevent other causes from infiltrating your system. For example, a proper time delay can keep the system from running due to discharged air still circulating in the system immediately after its operation. Another: it can allow the pressure controller to reset itself naturally while not calling for cooling as opposed to firing another cycle based on high pressure triggers due to compromised condensers.
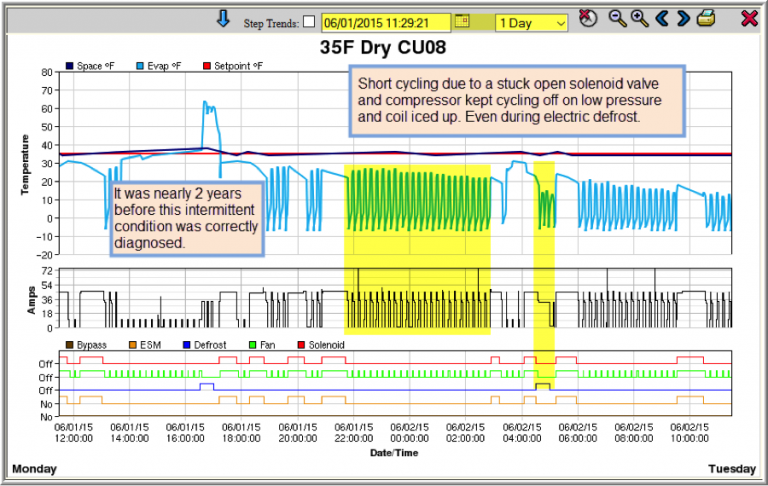
Here is a small handful of other causes: compressor valve leaking, no load capacity controls, low airflow, excessive refrigerant, discharge pressure too high.
Although it doesn’t have to be, early detection that your compressor is short cycling can be as difficult as figuring out what is the root cause. Why?
- In many facilities, the compressors are on the roof and we don’t have the opportunity to walk by our compressors and hear the sound of our compressors short cycling.
- For those whose compressors are located on a pad on the side of the building, our ears aren’t trained to identify such things.
- As depicted with a site in Figure 1, many refrigeration systems have redundant compressors for a refrigerated or frozen space which mask the issues of a compressor short cycling since the space is able to maintain the set temperature.
Now with the advent of IoT (Internet of Things), identifying your compressor is short cycling is possible through real time monitoring, control and data analysis. And given the cost of saved energy and potential product or inventory loss, these solutions have extremely cost effective and a must have.
We hope this blog post was informative in helping you troubleshoot a common issue in sub-optimally performing commercial refrigeration systems. Remember, it’s not enough to have a technician replace a malfunctioning part – the root cause of a short cycle must be determined and addressed to avoid future and potentially more serious problems.
Sources:
1. Ice Breaker: Compressor Short Cycling. ACHRNews.
2. Compressors Fail at Mild Temperatures. Michaels Energy.
Troubleshooting Chart. HVACRinfo.com.
Preventative Maintenance Techniques for HVAC/R Service Technicians. EPATest.com